Reclaimed Wood Floors
The growing popularity of reclaimed wood floors is a testament to the growing concern about the extensive use of natural resources. The beauty of reclaimed material lies in the minimal amount of processing that was used to create the lumber sometimes hundreds of years ago. Many of those materials possess stunning visuals due to age, sawing methods, and weathering.
A wide variety of materials are used in the production of reclaimed wood flooring. They range from wood procured from barns, homes, fences, and commercial buildings of all kinds. However, in the rush towards what many consider a healthy, there are questions about this method that must be considered.
Get the facts on Reclaimed Wood Floors
Limited availability is a major obstacle for reclaimed wood
Locating a supplier for the reclaimed material is the first step of the process. This may prove difficult, as availability can fluctuate wildly. Since sources and quality may vary, obtaining your reclaimed wood floor may require many months of searching.
The hidden challenges of reclaimed wood floors
Very little information can be found regarding what the reclaimed wood has been exposed to throughout its life. Paint containing lead and chemical treatments to preserve the wood can contain a number of hazardous chemicals. Many times, exposure to moisture may have promoted fungal growth and insect infestation. Topically applied chemical treatments for fungal, insect, or fire treatments, containing now-known health hazards, may also be found in reclaimed materials. Lastly, if the material is not properly re-dried, any insect infestation will remain active.
If the wood comes from a commercial building such as a foundry, traces of heavy metal or other residues from the manufacturing process could pose a risk. When using reclaimed materials they should be tested in a laboratory to ensure they do not contain any hazardous materials.
Are there any positive alternatives?
Due to the health concerns and unreliability of reclaimed wood, some homeowners considering reclaimed floors must explore other options. So the question must be asked, “Can the homeowner get the reclaimed look from new materials and still be environmentally responsible?” The good news is, “YES!” Today, there are hardwood collections that are environmentally friendly, fashionable, and designed to duplicate the aesthetics of reclaimed wood floors.
Hardwoods grown in the United States and Europe are being produced at a sustainable rate. In fact, the growth rate of American and European hardwood forests are currently exceeding the amount cut every year due to responsible/sustainable forestry practices.
Fabrication method of newly harvested Vs. reclaimed wood
In modern practices hardwood trees are typically cut and processed into 1” thick lumber. Many wood floor fabricators then take the lumber and dry it in a kiln to reduce the moisture content to a very stable level. They then mill the product flat and re-saw those materials to mimic reclaimed textures an visuals. This is a very different method than what was typically used in antiquity. Many logs were sawn by hand and stacked in an outbuilding to protect it from weather while the wood slowly air dried, sometimes for as much as one to two years. The result was more rustic, but lacked the stability provided by modern kiln drying methods.
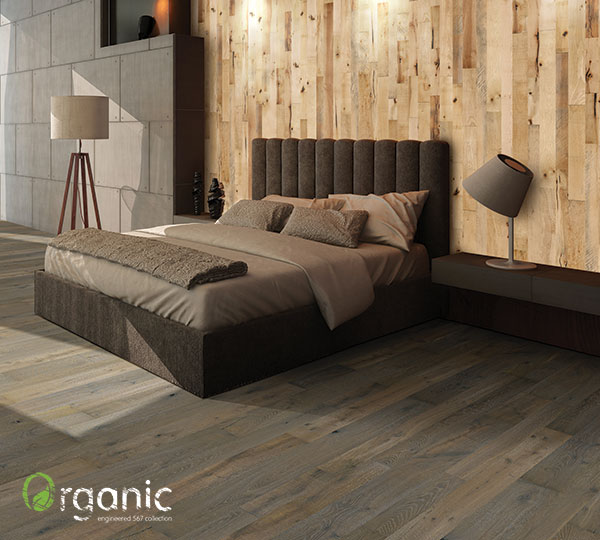
Organic 567 Gunpowder on the floor and Anise Organic Solid on the wall
What is the best option?
To create a realistic, reclaimed visual for wood floors, a variety of techniques must be employed. The first step is to green saw and dry the materials by air. This process is then finished by placing the material in a kiln. Kiln drying carefully controls the moisture removal process and kills any insects that may be in the wood. Milling the wood flooring with the green sawn texture still on the board is worth the effort due to the authentic look it produces. With newly harvested wood, the homeowner is getting the best of both worlds, by having wood floors that have the same visual characteristics and authentic look of reclaimed floors, while having them built with the stability and cleanliness of newly cut and manufactured floors.
What is available?
Organic Solid: Surface textures retain the green cut characteristics and patina only achieved during air-drying. Hallmark Organic Solid is offered in a ¾” thick, 3 ¼” and 4” random width, and random lengths up to 6’. A culmination of years of research has resulted in a completely unique method of flooring production.
Organic Engineered: Offers wider visuals in a 9/16” thick, 5”, 6”, and 7” random width, and random lengths up to 6’. With a 4mm sawn face, this offering takes the process to an even higher level of manufacturing expertise. The target introduction date for Organic Engineered is November 2015.
NuOil®: Both Organic Solid & Engineered are finished with Hallmark Floors’ proprietary, state of the art, two-stage hybrid oil system. Our NuOil® finish is ready to use straight from the box, stain resistant, and easy to maintain. Fusing 21st century technology with the methods of antiquity creates a winning combination for any home or décor.
All of Hallmark Floors Spotlight Dealer carry our Organic Collections
Author: Ron Oliver
Contributor(s): Ryan Oliver & Sylvia Bulanek